Understanding the differences between DTF and DTG printing is crucial for making an informed decision on which technology to adopt for your printing needs. DTF (Direct to Film) printing, a relatively new technique, involves printing designs onto a special film and then transferring them onto fabrics using heat and pressure. On the other hand, DTG (Direct to Garment) printing is a more established process where designs are directly printed onto the clothing item using inkjet technology.
The choice between DTF and DTG printing hinges on various factors such as the types of materials you wish to print on, the vibrancy and variety of colors you need, and the quantity of production. DTF printing excels with its ability to adhere to a wide range of fabric types and its flexibility for color use, whereas DTG printing is known for its quality, soft-hand feel, and feasibility for small batch orders.
Evaluating the operational aspects, DTG typically requires pre-treatment of garments and has a straightforward setup, making it user-friendly. DTF printing, while versatile in its application, involves extra steps such as applying adhesive powder and a melting process to ensure the transfer’s durability. Your choice will depend on the specific requirements of your print jobs and the scale at which you operate.
Overview of DTF and DTG Printing
Direct-to-Film (DTF) and Direct-to-Garment (DTG) are two prominent techniques in the textile printing industry. Each method brings its unique advantages to your fabric printing projects.
Defining DTF Printing
Direct-to-Film (DTF) printing involves printing a design onto a special film, which is then transferred to the fabric using a heat press. Here are the key steps in DTF printing:
- Print: Your design is printed onto a clear film with a special DTF printer.
- Powder Application: The film gets a coating of adhesive powder.
- Curing: The adhesive is melted and bonded to the ink via a curing oven or heat source.
- Transfer: The design is transferred to the fabric using a heat press. This technique allows for vibrant prints on a wide variety of fabrics and is especially useful for detailed designs that may be complex for other printing methods.
Defining DTG Printing
Direct-to-Garment (DTG) printing, on the other hand, involves printing designs directly onto the garment. Key aspects include:
- Pre-treatment: The garment, usually made of cotton, is pre-treated to ensure ink adhesion.
- Printing: An inkjet printer applies the design directly onto the garment.
- Curing: The print is cured with a heat press to set the ink.
DTG printing is ideal for short runs and detailed, multi-colored designs directly on cotton garments. It’s highly appreciated for its soft feel and detailed image quality.
Technical Comparison
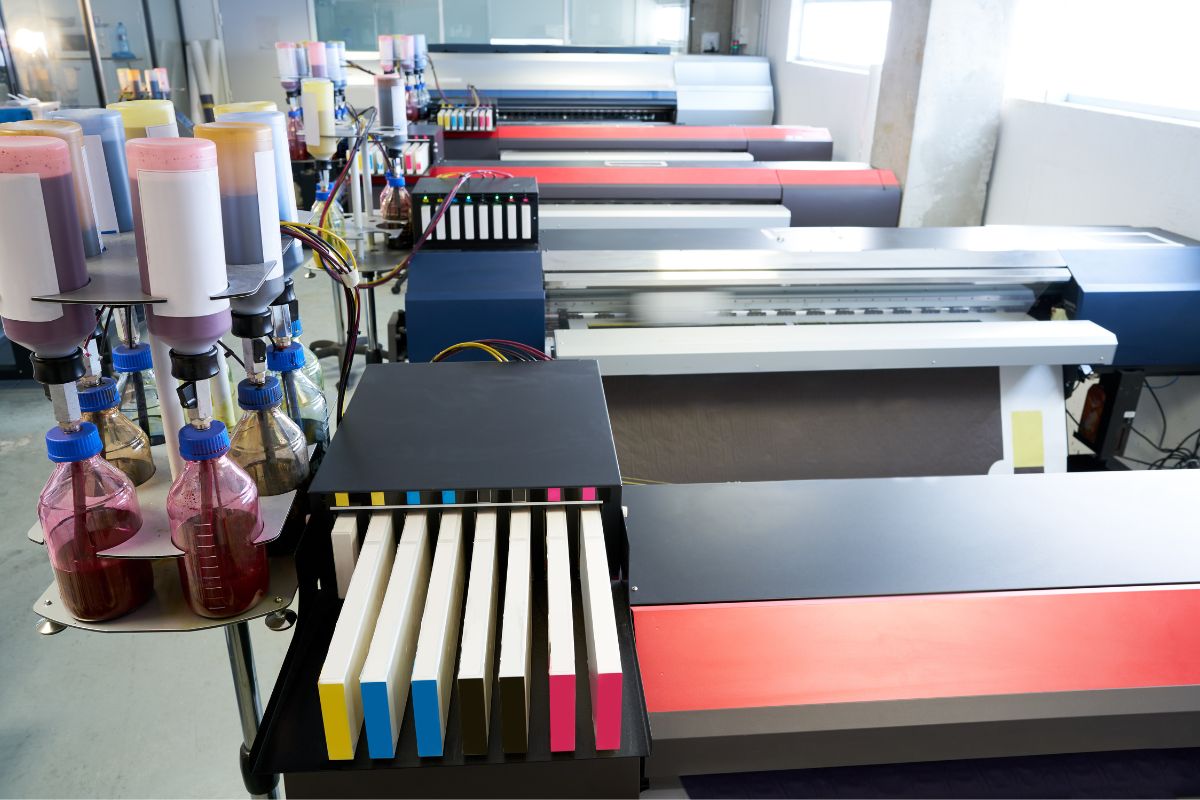
When evaluating DTG (Direct-to-Garment) and DTF (Direct-to-Film) printing methods, it’s essential to consider various technical aspects. These include the ink and printing process, the compatibility with different fabrics and materials, the efficiency of the production workflow, and the quality and output characteristics of the prints.
Ink and Printing Process
DTG: utilizes water-based inks which are applied directly to the fabric through inkjet technology. This method allows for detailed and precise printing with a capability for vibrant colors and color accuracy. However, it typically requires a pre-treatment of the fabric, especially when working with cotton garments.
DTF: involves printing a design onto a special transfer film that is then covered with an adhesive powder and cured. The print is later transferred using a heat press machine. DTF printing maintains color vibrancy without the need for fabric pre-treatment.
Fabric and Material Compatibility
DTG: excels on natural fabrics, like cotton, where it can soak into the fibers for a soft-to-the-touch feel. It has limited compatibility with polyester and nylon due to dye migration issues.
DTF: shines in its versatility, adhering well to a range of materials including natural and synthetic fabrics. This method extends the feasible product range, as it sticks to polyester, nylon, and blended fabrics effectively.
Production Workflow
DTG: involves a straightforward printing process directly on the garment, placed on a platen. It’s ideal for print-on-demand services but can be slower due to individual garment handling and the pre-treatment process.
DTF: streamlines production by allowing you to print multiple designs on a roll of film before transferring. This method can potentially increase throughput by separating the printing and pressing stages, advantageous for batch processing.
Quality and Output
DTG: is known for its high-quality prints featuring excellent texture and precision. The inkjet technology produces designs that are integrated into the fabric, which can result in a durable and long-lasting print.
DTF: offers robust print quality with good color vibrancy. As the design is transferred via film, it creates a slight elevation from the fabric, which can be felt to the touch. While it produces detailed designs, the texture differs from the softer finish of DTG prints.
Practical Considerations
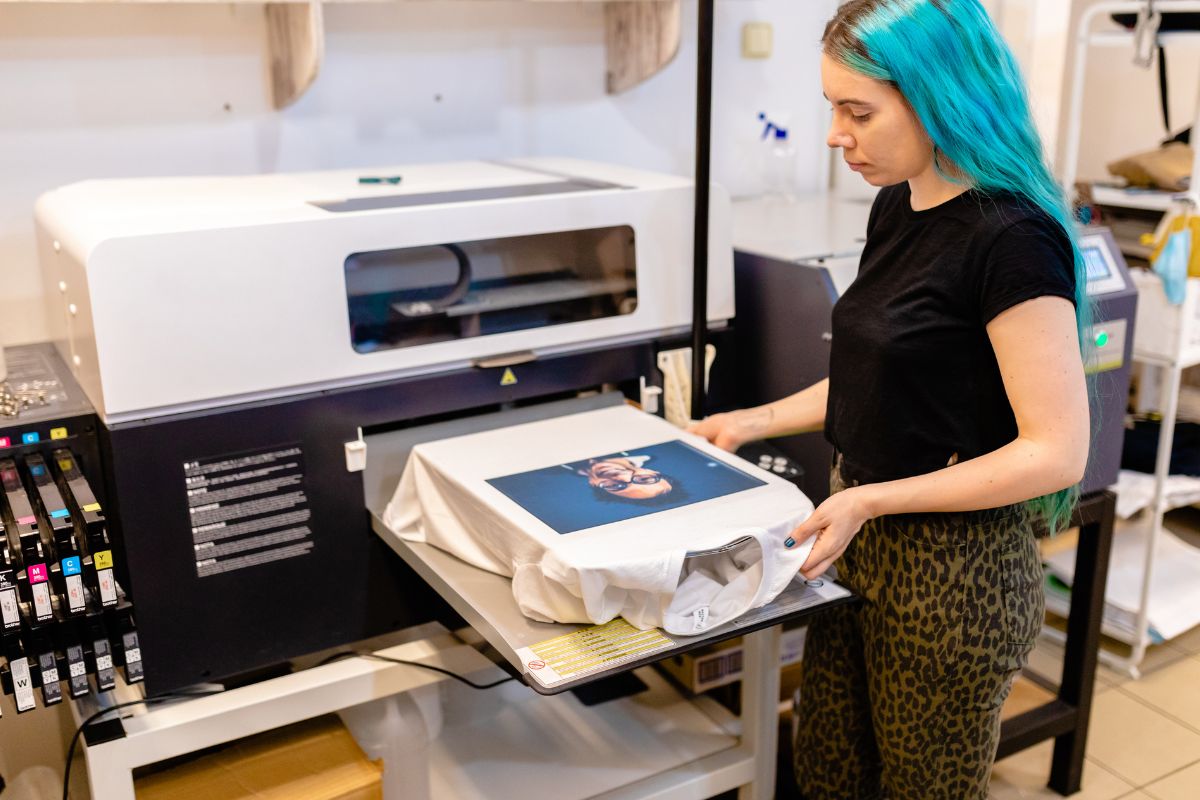
When evaluating Direct to Garment (DTG) and Dye Sublimation (DTF) printing methods for your custom apparel, it’s crucial you consider differences in cost, efficiency, and maintenance to make an informed decision.
Cost and Investment
The upfront investment for DTG printing can be significant, as it requires specialized printers and inks. However, it offers low production costs for small batches. Conversely, DTF might have a lower initial cost but could lead to higher expenses in bulk orders due to the cost of transfer films and additional materials.
Speed and Efficiency
DTG printers are praised for their production speed on small orders and their ability to produce full-color designs quickly. This makes them efficient for t-shirts, tote bags, and hoodies. DTF, on the other hand, allows for efficient layering of colors and is faster in processing bulk orders, which can be essential for time-sensitive projects.
Durability and Maintenance
In terms of durability, DTG prints are known for being long-lasting and typically offer good washability. Maintenance for DTG printers is critical to ensure their longevity. For DTF, print durability can also be high, but it may vary based on the adherence of the transfer film to the fabric.
Customization and Versatility
DTG stands out for its ability to easily print vivid and intricate designs, particularly on cotton fabrics. It is highly flexible, allowing for customization on a piece-by-piece basis. DTF also offers a versatility that includes working with a wider range of fabric suitability, extending beyond just cotton, which can be incredibly advantageous for diverse product offerings.
Industry Applications
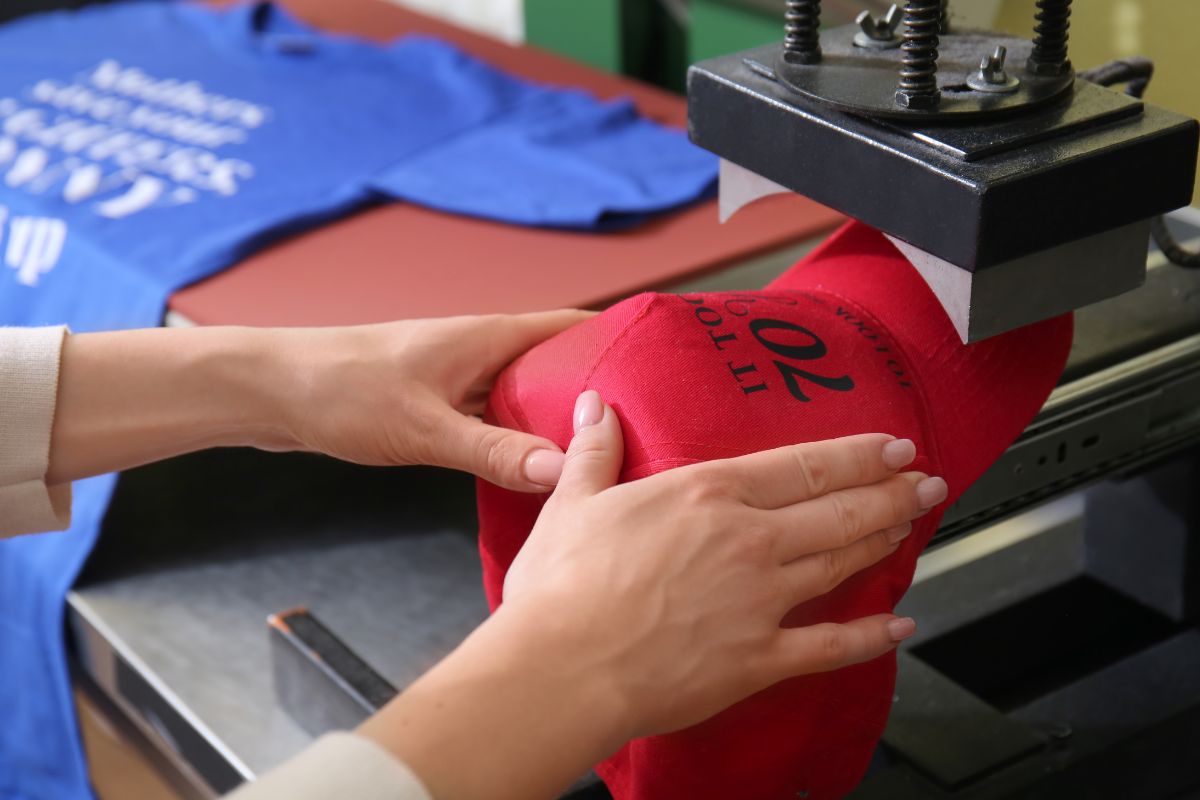
Direct-to-Garment (DTG) and Direct-to-Fabric (DTF) printing technologies have revolutionized the textile industry by enabling efficient production, whether it’s for single pieces or thousands. Understanding their distinct industry applications will inform your decision-making process for your garment printing needs.
Print-On-Demand and Small Runs
DTG printing excels in print-on-demand services and small production runs. This method is perfect for when you need custom apparel with vibrant designs or complex images on a short turn around. Labor costs are lower because the process requires minimal setup, meaning you can offer a diverse range of full-color prints without a significant increase in cost per item. Producing intricate details is where DTG stands out, and with no need for bulk orders, you maintain a lean inventory that responds to your customer’s demands.
Large Scale Production
For larger scale productions, DTF offers a solution where the balance of cost, efficiency, and quality intersect. Unlike DTG, DTF is suitable for high production volume because it allows for continuous printing, significantly reducing the per-unit cost for bulk orders. If you’re considering a large-scale application, a detailed cost analysis will show DTF overtaking DTG in terms of affordability when the number scales up. Although there’s a higher initial labor setup, the long production runs greatly diminish this factor’s impact on the overall cost.
Custom Apparel Trends
Keeping abreast with custom apparel trends means embracing technologies that allow freedom in design without sacrificing the quality of printed apparel. DTG and DTF both offer opportunities to capitalize on trends with rapid response times. DTG’s advantage lies in its ability to produce full-color prints and accommodate small-scale, niche market demands. DTF, on the other hand, is becoming increasingly popular for its ability to adorn a variety of fabrics, providing versatility to fulfill diverse market needs.
By analyzing and comparing these specific applications of DTG and DTF within the industry, you gain the knowledge to choose the right technology for your custom garment printing business’s unique demands.
Environmental and Health Considerations
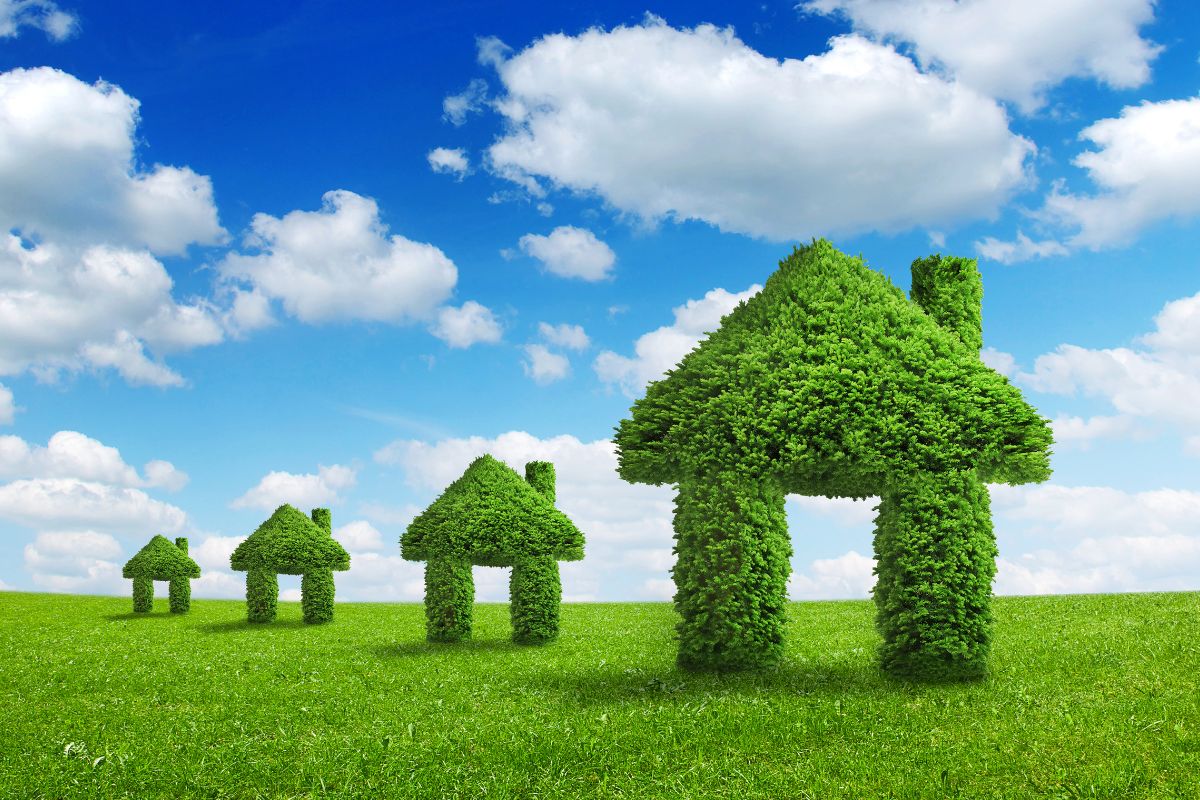
When assessing the environmental and health impact of Direct to Garment (DTG) and Direct to Film (DTF) printing technologies, it’s essential to examine ink safety and the sustainability of production processes. These factors directly influence the eco-friendliness of the products you use and their potential effects on health.
Ink Safety and Composition
Eco-friendliness and Non-toxic: In the realm of DTG and DTF printing, the safety of the inks used is paramount. You want to ensure that the inks are non-toxic and, ideally, eco-friendly. Some DTG inks are OEKO-TEX certified, which means they meet specific standards that make them safe to use on textiles that come into direct contact with skin.
Vegan inks: Consider whether the inks used are vegan, which indicates that no animal products or by-products are included and that the inks have not been tested on animals. This aspect is increasingly important to consumers who prioritize ethical considerations in their purchasing decisions.
Sustainability in Production
Efficiency and Fabric Limitations: Sustainable production is crucial for both DTG and DTF printing. The efficiency of the printing process can reduce waste and minimize energy consumption. DTG printers often have fabric limitations, typically requiring a high cotton content to ensure quality prints, which can influence the sustainability factor of your product line.
- Reducing Waste: DTF printing can allow for more diversity in substrates, potentially reducing fabric waste as it can be applied to a wider range of materials. Research the production methods of the printers to understand their waste output.
By focusing on ink safety, composition, and the sustainability of the production processes, you ensure that you choose a printing method that aligns with environmental and health standards. This conscientious approach benefits not only the planet but also the well-being of consumers and communities.
Frequently Asked Questions
When exploring the realms of DTG (Direct to Garment) and DTF (Direct to Film) printing techniques, you’ll encounter several recurring inquiries. The resilience, cost-effectiveness, and quality of the prints vary between these methods, each suited for specific needs and scale of production.
What are the main differences in durability between DTG and DTF printing techniques?
DTG printing infuses ink directly into the fabric, which typically leads to prints that last as long as the garment itself with proper care. On the other hand, DTF transfers a film onto the fabric, which may eventually peel or crack over time with washing and wear.
How do the costs compare when considering DTG printing versus DTF printing?
DTG printing generally involves higher initial equipment and maintenance costs but offers lower costs per print in the long run, especially suitable for small, custom orders. DTF printing, while it may have lower startup costs, can be more cost-efficient with medium to large runs due to its transfer process and bulk production capability.
Can DTG or DTF printing methods produce longer lasting prints?
DTG has the potential to produce longer lasting prints as the ink is more integral to the garment. However, DTF prints’ longevity has improved with advancements in transfer technology and when applied correctly, can also exhibit substantial durability.
Which printing technology yields better results for detailed designs, DTG or DTF?
DTG printing excels at reproducing highly detailed designs with a wide color spectrum directly on the garment, providing precise and vibrant prints. DTF also captures detail well but may slightly differ in texture and feel, with its additional layer between the ink and fabric.
How does the print quality of DTG and DTF compare against traditional screen printing?
DTG and DTF both offer superior print quality with multi-color and intricate designs compared to traditional screen printing. However, screen printing may still be favored for large volume orders of simpler designs due to its cost-effectiveness and ink durability.
In terms of operational efficiency, is DTG or DTF printing more advantageous for small-scale production?
For small-scale production or custom pieces, DTG printing is highly efficient as it requires minimal setup time per print, allowing for quick turnaround and the ability to print on-demand. DTF can be efficient for small runs as well, but it’s best leveraged when doing multiple prints of the same design.